Selecting the Right In-Mold Labeling Process for Your Packaging
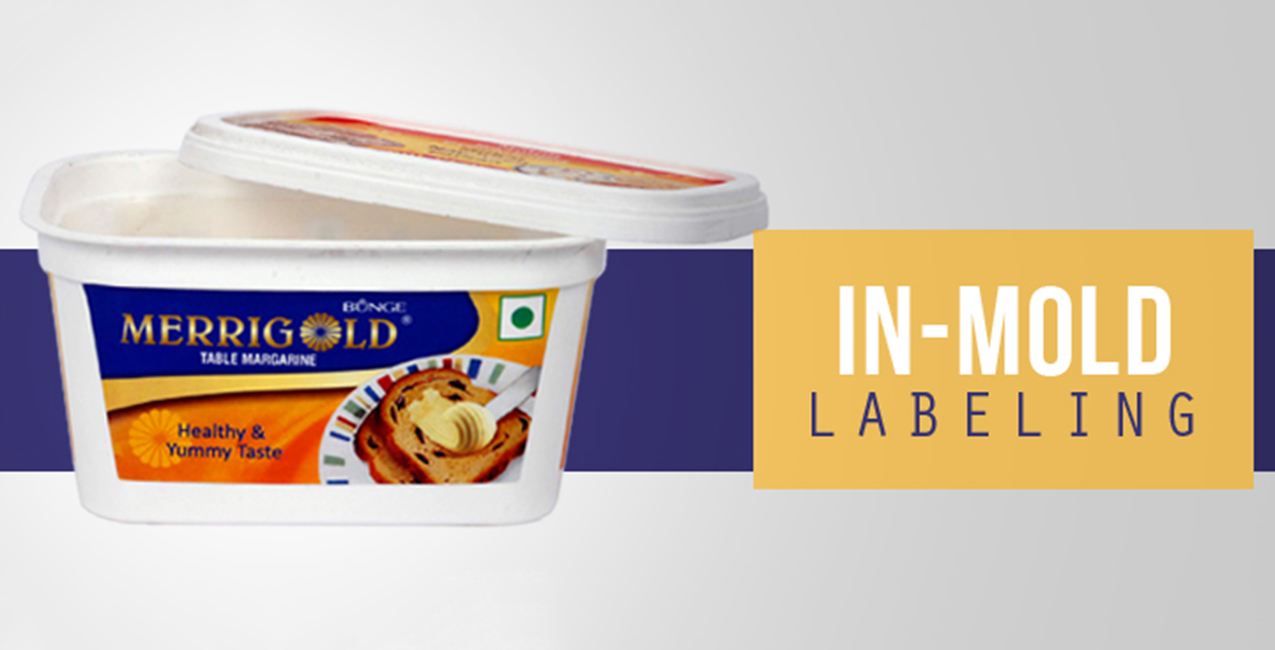
In-mold labeling is a process in which manufacturers place a pre-printed polypropylene label in the mold of the packaging during the manufacturing process. Hence, when the mold gives shape to the plastic packaging, it also adds the labeling to the packaging. The mold gives the shape to the end product as well as performs the labeling. After the curing time, the packaging and the labeling becomes a single piece. There are three methods of in-mold label printing processes. These include the injection molding, the blow molding and the thermoforming.
#1 - Injection Molding
Injection molding is the most common form of molding thermoplastics or thermosetting polymers. During this process, manufacturers inject heated and liquefied plastics or polymers in a mold. The mold generally has a small hole or opening through which the injection takes place. After the injection is done, the mold is allowed to cool where the plastic takes its shape. This is the way a lot of plastic containers a made. Butter or ice-cream tubs are very common examples of products that use injection molding as well as in-mold labeling.
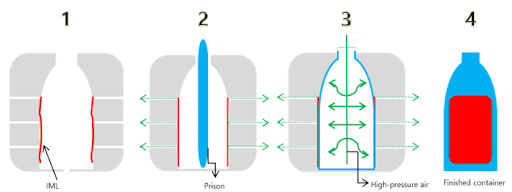
For example, the Amul Lite butter tubs, and a lot of skin cream packaging is made using this process. Smaller plastic paint buckets also use the same manufacturing process. Computer keyboards and cell phone keypads also use this manufacturing technology.
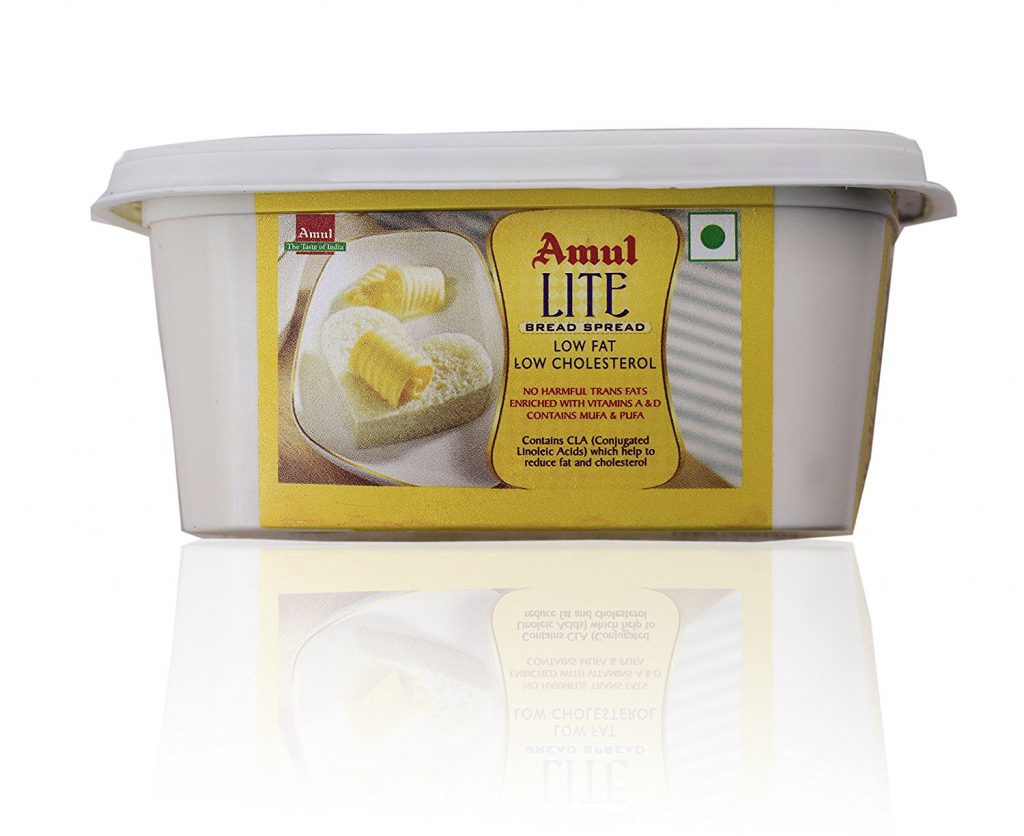
In case of injection method of in-mold label printing, the printed label is first placed into the mold and during the injection process, the printed polypropylene film fuses with the thermoplastic. So, in one step, we get the labelled plastic packaging.
#2 - Blow Molding
Blow molding is used for hollow plastic parts. This is a process in which manufactures stretch or extrude a heated plastic mass to take the shape of a mold. Blow molding is a very old process. Glass bottles used this manufacturing process and hence, even today, plastic bottles use the same principles of glass blowing. In blow molding, the extruded plastic is first put into a hollow tube. The hollow tube is captured in the mold and air is blown into the hollow tube so that it captures the shape of the mold. The inner wall of the mold contains the polypropylene sheet that has the labeling printed on it. As the plastic cools down, the labeling infuses into the mold.
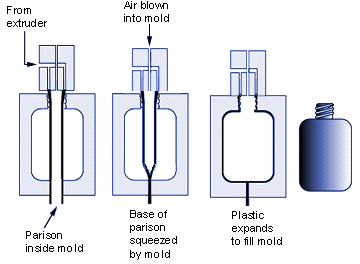
Manufacturers use this process to produce liquid containers, such as containers for liquid soaps, shampoos, dishwashing detergents, ketchup, and sauces. Most shampoo bottles on the market use this form of labeling as it is waterproof.
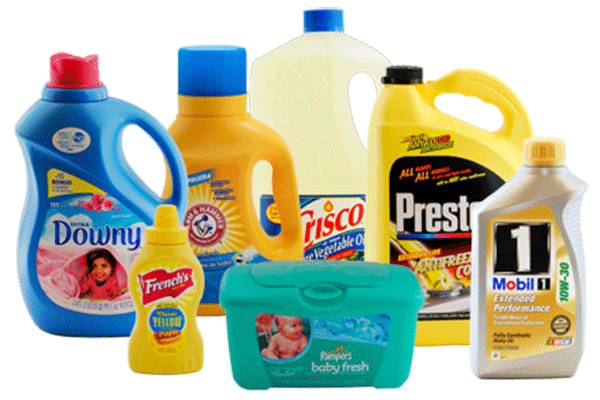
#3 - Thermoforming
Thermoforming is slightly different than the previous two processes as in this case, the plastic is not completely melted. Manufacturers use heated plastic sheets for the process. They use a forming tool that gives the plastic sheets the form of containers. Here, during the forming process, the preprinted labels accompany the plastic sheets. The heated sheets are stamped onto a mold and during this stage, the printed label and the plastic sheet binds together.
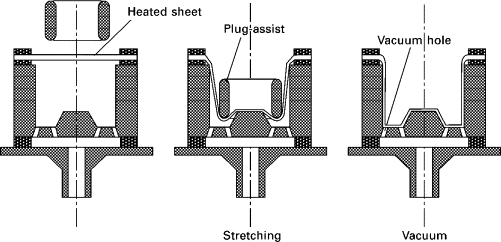
Manufacturers use thermoforming for making plastic cups. Ice cream cups, as well as plastic coffee cups, are made using this process. Also, plastic tubs used for packaging ice cream use this manufacturing process.
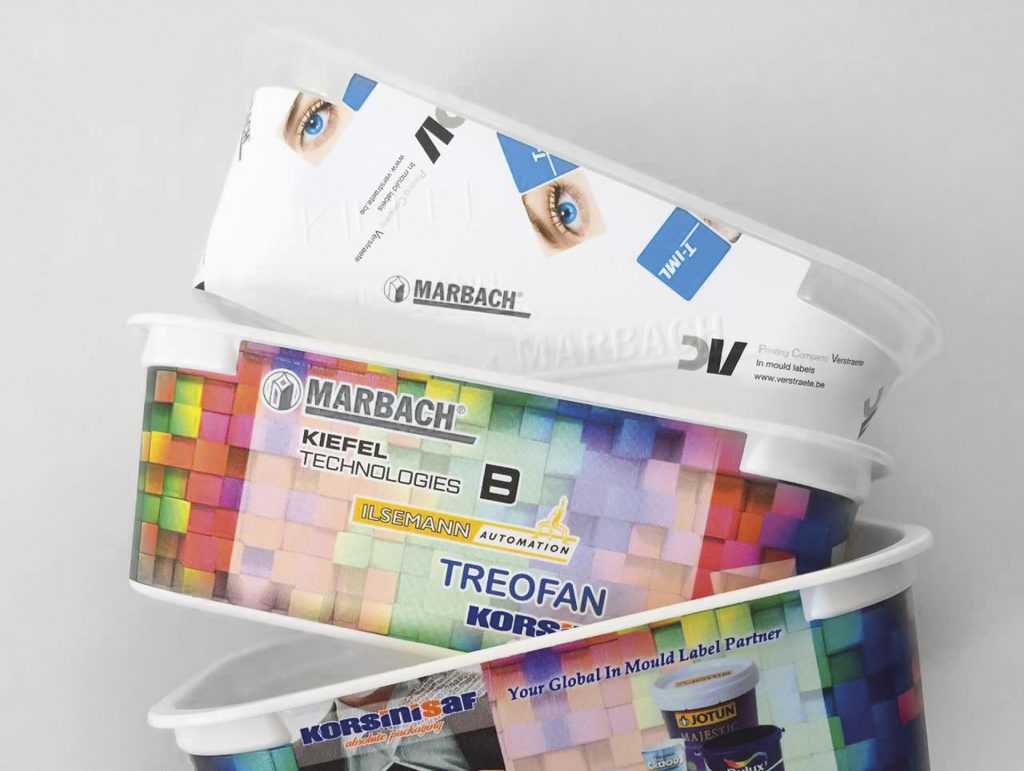
Pros and Cons of In-Mold Labeling
- Maximum coverage: With in-mold labeling, you can cover a lot more surface of the packaging with minimal effort. Moreover, this provides full-colour high-resolution graphics for your labeling.
- Wear resistance: Unlike separate labels, these labels do not face or tear away easily. They are a part of the plastic container itself. Hence, they are waterproof, resistant to fading and wear and tear.
- Minimal production time: There is no extra delay in labeling during the manufacturing process. The container is created and labelled in a single step. There is no need for storing unlabeled containers for later labeling, the containers do not have to be shipped to any other facility for labeling either.
- Environmentally friendly: The label and packaging make a single piece and hence recycling them are much easier.
- A wide range of customization options: There are multiple options when it comes to customizing the labels in in-mold labeling. Manufacturers can use multiple types of inks and paints for labeling.
- Fast changeovers: If you are changing the packaging label, then there is almost no extra cost associated with it. Incorporating a new design is quite easy and there is no loss of production during the change.
- Only available for thermoplastics: In-mould labeling is not available for glass, paper, or metallic containers.
Read: Detailed information about packaging design and development.
Wrap Up
In-mold labeling is a common and low-cost way to manufacture labelled containers quickly. The labeling is resistant to wear and tear and is also waterproof, making it a great option for labeling containers that are made from a mold.